دانستنیهای صنعت چسب
گریس چیست؟
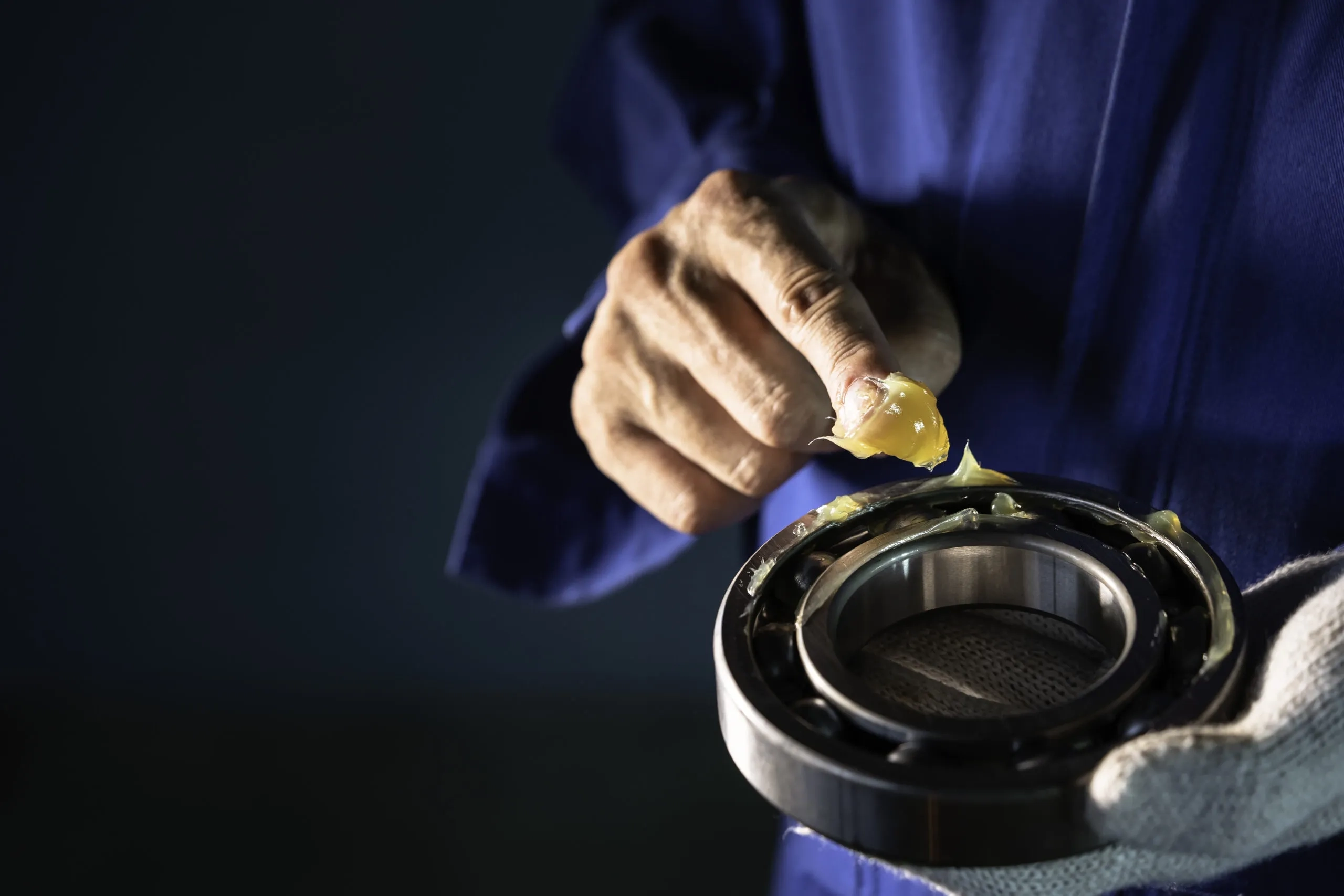
گریس یکی از مهمترین روانکارهایی است که امروزه در صنایع مختلف کاربرد گستردهای دارد. این ماده که از ترکیب روغن پایه، ضخیمکننده و مواد افزودنی بهدست میآید، توانسته است جایگاه ویژهای در میان روانکارهای صنعتی پیدا کند. عملکرد بالا، پایداری در دماهای مختلف و نگهداری سادهتر، از جمله عواملی هستند که گریس را نسبت به روغنهای روانکار متمایز کردهاند.
در این مقاله به معرفی کامل گریس، ساختار آن، تاریخچه، انواع مختلف، ویژگیهای کاربردی و مزایا و معایب آن خواهیم پرداخت. همچنین، جدول مقایسهای در انتهای متن قرار گرفته تا انتخاب نوع مناسب گریس با آگاهی بیشتری انجام شود.
برای دیدن محصولات صنعتی ما روی لینک کلیک کنید.
فهرست مطالب
- تعریف گریس و ساختار آن
- تاریخچه پیدایش گریس
- اجزای تشکیلدهنده گریس
- انواع گریس بر اساس پایه صابونی
- کاربردهای صنعتی گریس
- مزایا و معایب استفاده از گریس
- جدول مقایسهای
- جمعبندی و توصیه نهایی
تعریف گریس و ساختار آن
گریس، ترکیبی نیمهجامد یا جامد است که از امتزاج روغنهای پایه معدنی یا سنتتیک با مواد ضخیمکننده و افزودنیها ساخته میشود. این ترکیب به عنوان روانکار در شرایطی که روانکاری با روغن به سختی انجام میپذیرد، نقش کلیدی ایفا میکند.
بهطور خلاصه، گریس همان روغن روانکار است که با کمک یک ماده ضخیمکننده به شکل جامد یا خمیری درآمده است. این ویژگی باعث میشود که گریس به راحتی در محل مورد نظر باقی بماند و خاصیت روانکاری خود را حفظ کند.
تاریخچه پیدایش گریس
ریشه واژه “گریس” به واژه لاتین crassus به معنی چربی بازمیگردد. در قرن نوزدهم، نخستین گریسها به روش سرد و با پایه کلسیم تولید شدند. در آن زمان ترکیب صابونهای حیوانی با روغنهای معدنی، گریسهایی تولید میکرد که برای وسایل نقلیه با سرعت پایین کاربرد داشتند.
با گذشت زمان و توسعه ماشینآلات صنعتی، نیاز به گریسهایی با مقاومت بیشتر در برابر گرما و فشار احساس شد. از اینرو ساخت گریسهای جدید با استفاده از صابونهای پیچیدهتر، مواد افزودنی و روغنهای پایه مقاومتر شکل گرفت.
اجزای تشکیلدهنده گریس
تمامی گریسها از سه جزء اصلی تشکیل شدهاند:
۱. روغن پایه (Base Oil)
روغن پایه، بخش روانکار اصلی گریس است و معمولاً از منابع معدنی، سنتتیک یا بیولوژیک بهدست میآید. روغنهای معدنی به دلیل قیمت مناسب و عملکرد قابل قبول در اکثر گریسها بهکار میروند.
۲. ضخیمکننده (Thickener)
ضخیمکننده ساختار جامد یا نیمهجامد گریس را ایجاد میکند. انواع ضخیمکننده شامل صابونهای فلزی مانند لیتیوم، کلسیم، سدیم، آلومینیوم و همچنین مواد غیرصابونی مثل بنتونیت و سیلیکا هستند. گریسهای کمپلکس که از ترکیب صابون فلزی و یک عامل پیچیده ساخته شدهاند، توان تحمل حرارت و بار بیشتری دارند.
۳. افزودنیها (Additives)
افزودنیها نقش بهبوددهنده خواص را دارند. آنها میتوانند مقاومت در برابر اکسید شدن، زنگزدگی، فشار بالا و اصطکاک را افزایش دهند. افزودنیهای ضدسایش و آنتیاکسیدانها از جمله رایجترین ترکیبات افزوده شده به گریس هستند.
انواع گریس بر اساس پایه صابونی
در صنعت، گریسها بر اساس نوع ضخیمکننده دستهبندی میشوند که هر کدام ویژگیهای خاص خود را دارند:
گریس کلسیم
اولین نوع گریسهای صنعتی، با ویژگی ضدآب بودن و قیمت مناسب. مناسب برای دماهای پایین تا متوسط (حدود ۶۰ درجه سانتیگراد).
گریس سدیم
قابل استفاده در دماهای بالاتر، اما فاقد خاصیت ضدآب بودن. به دلیل قیمت پایین هنوز در برخی صنایع استفاده میشود.
گریس لیتیوم
یکی از رایجترین انواع گریس در جهان. ویژگیهایی همچون تحمل دمای بالا، مقاومت در برابر شسته شدن و مناسب برای روانکاری عمومی دارد.
گریس آلومینیوم
مناسب برای دماهای بالا و محیطهای خاص. نسبت به سایر انواع قیمت بالاتری دارد اما عملکرد فوقالعادهای دارد.
گریس پلی اوره
فاقد صابون فلزی، با مقاومت بالا در برابر اکسید شدن. مناسب برای روانکاری طولانیمدت در بلبرینگهای الکتریکی.
کاربردهای صنعتی گریس
گریس به دلیل ماهیت نیمهجامد خود، در بسیاری از شرایطی که استفاده از روانکار مایع مانند روغن امکانپذیر نیست یا به صرفه نیست، انتخاب ایدهآلی محسوب میشود. برخلاف روغنها که نیاز به روانکاری مکرر دارند، گریس در محل باقی میماند و میتواند برای مدت طولانیتری نقش روانکاری را ایفا کند.
در ادامه، مهمترین کاربردها و مزایای استفاده از گریس در صنایع مختلف را مرور میکنیم:
-
روانکاری ماشینآلات با دسترسی سخت: در بسیاری از موارد مانند موتورهای نصبشده در ارتفاع، خطوط محرکه، بلبرینگهای داخلی یا قطعاتی که باز کردن آنها نیازمند توقف خط تولید است، استفاده از گریس به دلیل کاهش دفعات روانکاری، کاهش هزینهها و افزایش بهرهوری را به همراه دارد.
-
ایجاد مانع در برابر گرد و خاک و آلودگیها: گریس مانند یک سد عمل میکند و اجازه ورود ذرات معلق یا خروج روانکار از قطعات را نمیدهد. این ویژگی در محیطهای آلوده یا کارخانجات صنعتی بسیار مهم است.
-
افزایش عمر کاسهنمدها و بهبود آببندی: روانکاری کاسهنمدها با گریس، نسبت به روغن هزینه کمتری دارد و از هدررفت انرژی ناشی از اصطکاک نیز جلوگیری میکند. درواقع گریس موجب کاهش اصطکاک اضافی میشود که معمولاً در کاسهنمدهای روغنی دیده میشود.
-
پایداری بیشتر نسبت به روغن در طول زمان: برخی گریسها بهگونهای طراحی شدهاند که حتی در صورت توقف دستگاه، در محل باقی میمانند و وظیفه روانکاری را تا پایان عمر قطعه انجام میدهند. این ویژگی بهخصوص در تجهیزات با توقفهای طولانی کاربرد دارد.
-
جلوگیری از زنگزدگی قطعات بلااستفاده: زمانی که قطعهای برای مدت طولانی مورد استفاده قرار نمیگیرد، گریس میتواند نقش ضدزنگ و محافظتی ایفا کند و از اکسید شدن فلز جلوگیری کند.
-
کارایی مناسب در مجاورت با آب: برخی گریسها بهویژه نوع لیتیومی یا کلسیم کمپلکس، خاصیت ضدآب دارند و در محیطهای مرطوب یا تماس مستقیم با آب عملکرد خوبی از خود نشان میدهند.
-
کاهش اصطکاک در زمان راهاندازی دستگاهها: برخی از گریسها بهگونهای طراحی شدهاند که در لحظات ابتدایی راهاندازی دستگاه، کمترین اصطکاک ممکن را ایجاد میکنند. این ویژگی از سایش اولیه جلوگیری میکند.
-
کاهش صدا و ارتعاشات مکانیکی: گریس مانند یک لایه نرم بین قطعات متحرک عمل میکند و باعث کاهش نویز و لرزش در دستگاههایی مانند چرخدندههای بزرگ، گیربکسها و نقالهها میشود.
-
عملکرد بهتر در شرایط سخت عملیاتی: گریس در دستگاههایی که در فشار زیاد، دمای بالا، شوکهای مکانیکی و سرعت پایین کار میکنند، کارایی بهتری نسبت به روغن دارد. بهویژه در یاتاقانهایی که چرخش معکوس دارند یا تحت ضربات مداوم هستند، گریس گزینهای مطمئنتر محسوب میشود.
-
بهبود عملکرد در محیطهای دارای خوردگی و سایش بالا: گریسها با ایجاد یک لایه محافظ، از تماس مستقیم فلز با فلز جلوگیری کرده و عمر قطعات را افزایش میدهند.
-
پایداری در دماهای متغیر: برخلاف بسیاری از روغنها که دمای کاری محدودی دارند، اغلب گریسها در دماهای گستردهتری قابل استفاده هستند، از دماهای زیر صفر تا بیش از ۲۰۰ درجه سانتیگراد (در نوع کمپلکس).
-
سادگی در طراحی قطعات: استفاده از گریس در طراحی بوشها و یاتاقانها، ساختار آنها را سادهتر کرده و هزینه تولید را کاهش میدهد. در مقابل، روانکاری با روغن نیازمند طراحی پیچیدهتر، لولهکشی، پمپ و خنککننده است که هزینه بالاتری دارد.
برای خرید گریس مگا 200 گرمی روی لینک کلیک کنید.
مزایا و معایب استفاده از گریس
روانکاری با گریس مزایا و محدودیتهایی دارد که شناخت آنها به انتخاب درست کمک میکند:
مزایای استفاده از گریس
- ماندگاری بالا و چسبندگی مناسب به سطح
- ساده بودن مصرف، به خصوص در قطعات با دسترسی سخت
- قابلیت آببندی قطعات و جلوگیری از نفوذ گرد و خاک
- کاهش دفعات روانکاری مجدد
معایب استفاده از گریس
- نداشتن قابلیت خنککنندگی مثل روغن
- عدم نفوذ به قطعات بسیار ریز
- مشکل در حذف کامل گریس قدیمی قبل از اضافه کردن گریس جدید
جدول مقایسهای مزایا و معایب گریس
ویژگیها | مزایا | معایب |
---|---|---|
قابلیت ماندگاری | بالا و ماندگار در محل | ممکن است در دماهای خیلی بالا تخریب شود |
قابلیت خنککنندگی | ضعیف | نسبت به روغن صنعتی، خاصیت خنککنندگی ندارد |
سهولت استفاده | روانکاری آسان در شرایط سخت | نیاز به دستگاه مخصوص برای روانکاری دقیق |
قابلیت آببندی | جلوگیری از ورود آلودگی و آب | در صورت استفاده نادرست، باعث گرفتگی میشود |
هزینه نگهداری | کاهش دفعات سرویس | نیاز به انتخاب دقیق نوع گریس دارد |
جمعبندی و توصیه نهایی
در پایان باید گفت که گریس به عنوان یکی از اجزای جدانشدنی روانکاری صنعتی، نقش مهمی در افزایش طول عمر قطعات، کاهش اصطکاک و بهبود عملکرد ماشینآلات دارد. انتخاب درست نوع گریس، بر اساس نوع کاربرد، دمای کاری، فشار وارده و نوع یاتاقان یا بلبرینگ، اهمیت زیادی دارد.
برای بلبرینگها و یاتاقانهایی که در معرض گرما، فشار یا شرایط محیطی سخت هستند، گریسهایی مانند لیتیوم کمپلکس یا پلی اوره میتوانند انتخابهای مناسبی باشند. در عین حال، برای کاربردهای سادهتر و ارزانتر، گریسهای پایه کلسیم یا سدیم هم گزینههای قابل قبولی هستند.
مجتمع چسب ایران با ارائه انواع گریس صنعتی، آماده تأمین نیاز مشتریان در حوزههای مختلف صنعتی و خودرویی است. برای دریافت مشاوره و خرید گریس با کیفیت مناسب میتوانید با کارشناسان ما در تماس باشید.
برای مشاهده قیمت چسب ها و خرید چسب و سایر محصولات چسب ایران به صفحه فروشگاه سایت مراجعه کنید.